Getting the most out of FireShield®
- Optimum performance of FireShield is achieved when it is placed as the outermost layer of the laminate, closest to the heat loaded region.
- Industrial grade epoxy, polyester and vinyl ester resin systems are compatible with FireShield
- FireShield may be used in standard composite manufacturing processes., these include hand lay-up, vacuum bagging, Vacuum Bag Resin Infusion (VBRI), RTM Lite, RTM, pultrusion and autoclave (prepreg) processes
- FireShield is to be treated in the same manner as a reinforcement ply located on one or both outermost surfaces of the laminate.
- FireShield may also be used to encapsulate the entire surface of the composite .
- Fire, smoke and toxicity screening tests should be performed in accordance with test specifications for the application requirement. Usually, the test specimen thickness is to be no thicker than the minimum thickness for the application
- Any cosmetic coating (paints, adhesives, resins, etc) applied after fabrication will hinder the performance of FireShield. If the finished part is to have a cosmetic coating of any kind, the specimen must be subjected to screening tests in the as-finished condition to confirm whether the part meets the specification requirements
- FireShield materials should always be stored in sealed polyethylene bags to reduce damage, contamination of surrounding chemicals and moisture absorption. FireShield left out of the protective pack may pick up moisture, causing blisters in the final product
- Only one ply of FireShield is necessary to protect the region requiring fire protection. Multiple layers of FireShield should not be applied sequentially in the part lay-up
- In regions where two or more plies of FireShield meet due to geometry constraints, a minimum overlap of 1 mm must be maintained. It is crucial that all surfaces requiring fire protection are covered with FireShield. If for some reason there are regions that cannot be physically covered with FireShield, an intumescent coating must be applied after the part is fabricated.
If you are looking for manufacturing guidelines head this way!
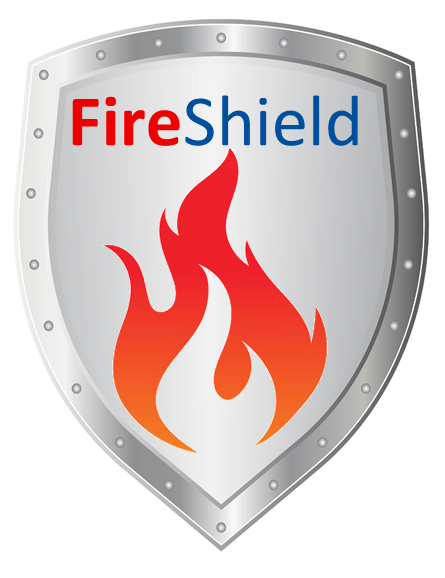
Some Points that may need to be considered
Thermal Performance
- Fire Performance below 800C – Theoretical calculations can provide indicative design information, but prototype testing is needed to confirm fire performance; For Single laminate: Expect Char thermal conductivity = 0.04-0.07 J/m.K.
- Fire Performance above 800C – Above 800C the relevant properties of a surface layer include self extinguishment and integrity retention. See Article – Higher Temperature applications.
Non-Structural Laminate
- Where FireShield® is replacing an existing surface tissue, bulking of the material in die or mould is unlikely to be a concern. Potential maximum compression of the substrates, without FireShield® chemical, is Glass Tissue 5% and Glass Cloth – plain or satin 8%
For Structural laminates,
- As the outer plies are not usually considered to contribute to the physical properties of a laminate, no impact is expected on designed strength, stiffness or TG from the use of a FireShield® layer. Surface hardness should be tested, to ensure that significant chemical “wash” into the resin that moves through the FireShield® to the face, has not occurred during manufacture.
Intumescent Chemical Types
A range of chemical types & substrates provides fire protection for most composite laminates, whilst allowing optimum laminate strength and stiffness – no filling required in the base resin.
FireShield® W
Based on ammonium polyphosphate, but a non-hygroscopic form of the product, so it can also be used in exterior applications where weathering may be a concern.
FireShield® HT-W
A form suitable for the higher temperature (HT) curing epoxy resins, common in aerospace, subject to weathering.
FireShield® ATH (Aluminium TriHydrate)
When an ATH-filled composite is subjected to temperatures above 230°C/446°F, the ATH exfoliates 35 per- cent of its weight as water while the remainder becomes inert (noncom- bustible) aluminumm oxide (Al₂O₃). This reaction is endothermic, or heat absorbing; the water acts as a heat reducing agent to hinder fire spread.
FireShield® MDH (Magnesium Hydroxide)
MDH decomposes at a higher temperature than ATH, making it useful when working with engineering thermoplastic resins, such as polyamides and polyprololene.
Substrate Types
A glass fibre reinforced substrate provides the mechanical strength and thermal properties for use.
Our substrates can be divided into two types: non woven (glass 30/35gsm + 60gsm), and woven (plain or satin weave 130gsm). We are currently testing a p-aramid 68gsm drapeable felt for 3D curves. Each type provides varying strength and cost with wovens having a tendency to shed.
Both satin and plain weave glass cloth substrates exhibit some degree of chemical shedding, as the glass area available for bonding is lower than is the case with tissue. The degree of shedding, at around 2% of gross weight, is not sufficient to impact on the fire protection, nor does it provide any health hazards, but it is unacceptable in clean-room situations. In such cases, the FireShield® can be converted into a Pre-Preg form.
Using FireShield® as a pre-preg has the advantages that it eliminates chemical shedding, and provides a material with tack, convenient for vertical lay-ups.
Regina can arrange for pre-preg manufacture, with the resin nominated by the client. Shelf life can be preserved by transporting the rolls in dry-ice packs, or by using refrigerated containers.
Post Production Practices
INSTALLATION OF FIRESHIELD® PROTECTED LAMINATES
FireShield® is a surface protecting material. If flame, during a fire, can reach unprotected parts of a laminate, fire protection is compromised.
During installation, consider all:
Edges and overlaps
Penetration and Fastenings
Welding and other joinings
Surface or through thickness intrusions
If the laminate surface is damaged or holes are drilled through the thickness such that resin/fibres are exposed, an intumescent coating/paint must be applied over that region to protect the exposed resin/fibre.
The following intumescent coating suppliers have products that have been tested successfully with FireShield®. Review the technical data sheets and SDS from the suppliers for procedures on how to use these coatings. The two tested intumescent coatings are:
Firefree 88
Distributor: Brenntag Australia Pty. Ltd.
Headoffice: 260-262 Highett Road, Highett VIC 3190 with branches in Brisbane, Sydney and Perth.
Tel: +61 3 9559 8333 Fax: +61 3 9532 0802 Email: info-aus@brenntag-asia.com
NoFire
Distributor: NQ Fire Protection Pty Ltd
3 Scott Street, Cairns, QLD 4870, Australia – Tel: 1 300 666 447 – Email: nofire@nqfire.com
Installation, edges, corners, joinings – welds, bolts etc.
Where structural sections of FireShield® protected laminate are joined to other materials, any potential flame path must be closed by applying a fireproof mastic. Where the laminate comes against other materials, brick, steel, flashings etc., any potential flame path must be closed by applying a fireproof mastic.
The following mastic product has been tested successfully with FireShield®.
Review the technical data sheets and MSDS from the supplier for procedures on how to use this sealant.